URETEK Deep Injection® Solves Pavement Fatigue in San Jose
Problem
The city of San Jose, California, experienced fatigue cracking in sections of roadway dedicated to municipal transportation bus lines. Originally, the blame was placed on low-quality materials in the asphalt composition. It was thought that these poor materials could not withstand the full weight of city buses frequently approaching and stopping in the same areas. Although the city attempted several traditional methods to fix the problem, the failures continued and the costs for repeated overlays and expensive full-depth repairs grew. The city then speculated that it was in fact the weak base and subbase that was contributing to the failure of the pavement and decided to pursue an alternative repair method. San Jose city officials asked URETEK to assess fatigue cracking found on sections of roadway dedicated to municipal transportation bus lines to determine if the URETEK Deep Injection® (UDI) process would provide a cost-effective, long-term solution.
Analysis
URETEK provided a preliminary design plan indicating one level of UDI injections spanning a 10-foot by 100-foot area. Upon arrival, URETEK preformed Dynamic Cone Penetrometer (DCP) testing to gather soil data and confirm the injection plan. The DCP test results confirmed the theory of weak subbase and subgrade soils and pinpointed the issues at depths between two and nine feet.
Solution
The DCP data prompted URETEK to modify the initial design to include an additional injection level to properly stabilize the work area. But before work could commence on the pavement preservation project, URETEK had to meet strict environmental requirements and comply with various city standards. Material engineers for San Jose worked closely with the URETEK Project Manager to thoroughly investigate and qualify URETEK’s unique polymer blend for city approval. Engineers concluded that the URETEK materials exceeded the requirements. With complete city approval, the UDI project was completed entirely from mobilization to clean-up in less than six hours.
Result
The results of the study were published (Ashtiani, et al. “Precast Concrete Panels for Rapid Repair of Airfield Rigid Pavements”) and briefed during the 90th Annual Meeting of the Transportation Research Board in Washington, DC, in January 2011. Precast panels installed with HDP performed better than those installed with flowable fill as a leveling material. Precast panels installed with UDI performed better than those installed with conventional injection. Therefore, the results of the study indicate that combining an HDP leveling material with UDI is the best method to install precast concrete repair panels.
URETEK Deep Injection® (UDI)
DCP test results were able to confirm that weak soils contributed to flexing of the pavement under the immense weight of the repetitive loading and unloading. URETEK’s intervention strengthened the weak soils, which increased the load-bearing capacity of the pavement and consequently extended the pavement lifespan. UDI solved San Jose’s problem by addressing the underlying cause of pavement failure. Thanks to URETEK, the city of San Jose successfully addressed their fatigued roadways in a faster and more cost-effective manner than traditional repair methods.
URETEK 486 Star®
URETEK 486 Star® polymer is a two-component, high-density, expanding thermoset polyurethane system. It was developed to be the ideal solution for under-sealing, void filling, lifting of settled pavement, stabilization and stiffening of weak soils, and for encapsulating and sealing buried infrastructure. URETEK 486 Star® is environmentally inert, non-toxic, and resists underground water erosion or weakening due to its industry-leading hydrophobic properties.
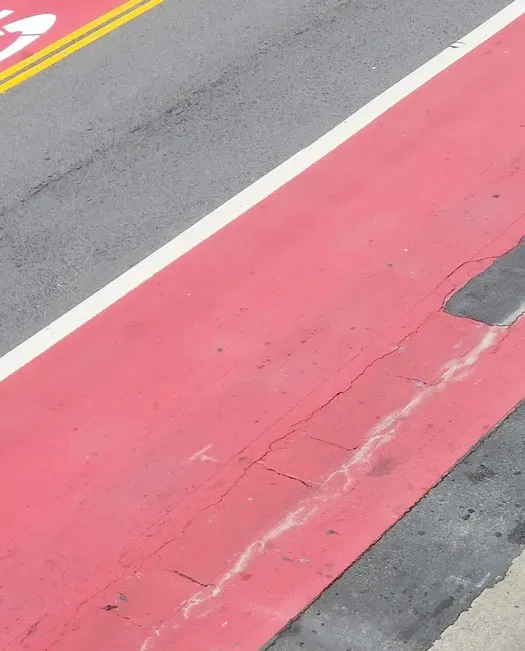
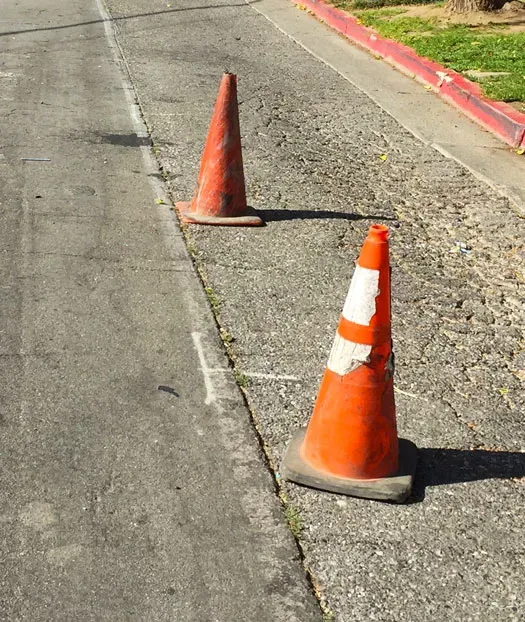
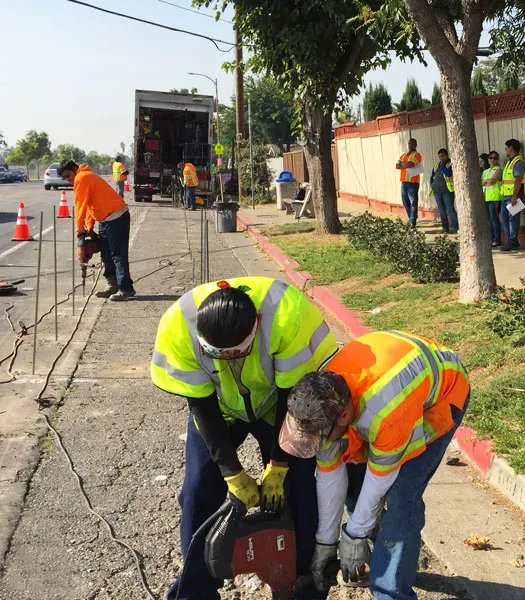