Railway Subgrade Repair using URETEK Deep Injection®
Problem
Today, 40% of the world’s freight cargo is transported via rail making the structural integrity of railways and their substructures essential. Weak or compromised rail substructure can lead to track instability, transit slowdowns, train derailments, ballast fouling, and differential track deflection. Maintenance activities to prevent these outcomes are very important and commonplace for railroad substructure systems, but they come at a cost. Track maintenance in areas with weak subgrades is especially expensive because ballast replacement, tamping, and track realignment are often required. URETEK teamed with the University of Wisconsin – Madison to determine if URETEK Deep Injection® (UDI) could offer a cost-effective way to improve weak subgrade and in turn increase overall track stiffness. They performed their testing on a section of side track operated by Wisconsin and Southern Railroad in Madison, Wisconsin.
Analysis
The University of Wisconsin – Madison provided detailed deflection and geophysical measurements of the site before and after treatment, and URETEK provided Dynamic Cone Penetrometer (DCP) logs to indicate soil strength. The track stiffness, or modulus, was also measured before and after UDI treatment. (Modulus is a key measure of the health of a rail’s superstructure and substructure; increasing modulus leads to less track deflection under train loading, fewer track misalignment problems, and lower operating costs.)
Solution
URETEK treated a 50-foot section of track with UDI. The injections of polyurethane were set at two depths: at four feet to strengthen the railway structure and at six feet to strengthen and stiffen the soft subsurface material. Due to restrictions on the railroad at the test site, UDI could not be performed within 30 centimeters of the bottom of the tie.
Result
The UDI treatment increased track stiffness by 90% (track modulus increased from eight MPA to 15.4 MPA). This improvement in track stiffness increased the overall track rating from “poor” to “average.” URETEK, Wisconsin, and Southern Railroad conducted a life cycle cost analysis with inputs from a ten-year period. Over this period, using UDI as opposed to traditional maintenance resulted in a cost savings of $1,000 – $20,000, depending on discount rate. This test proved that URETEK can offer railways a way to provide significantly longer service life at a significantly lower maintenance cost. The success of this project in improving track stiffness demonstrates that UDI can improve weakened subgrade and provide a viable alternative to costly rail maintenance.
URETEK Deep Injection® (UDI)
Widely referenced throughout our industry, UDI involves the injection of structural polymer into base and subgrade soils to increase the load bearing capacity. This is achieved by injecting the polymer through small holes drilled directly through the pavement structure to depths determined by site-specific analysis. Our URETEK 486 Star® material flows easily into voids and weak zones within the soil mass below. Through a controlled chemical reaction, the expanding polymer compacts surrounding soils and applies a controlled pressure on targeted areas of the affected pavement above. If needed, a multi-injection design plan is utilized to gently return the pavement to its original grade. The composite material quickly cures into a strong, dimensionally stable, and water-resistant geo-material, providing years of reliable service.
URETEK 486 Star®
URETEK 486 Star® polymer is a two-component, high-density, expanding thermoset polyurethane system. It was developed to be the ideal solution for under-sealing, void filling, lifting of settled pavement, stabilization and stiffening of weak soils, and for encapsulating and sealing buried infrastructure. URETEK 486 Star® is environmentally inert, non-toxic, and resists underground water erosion or weakening due to its industry-leading hydrophobic properties.
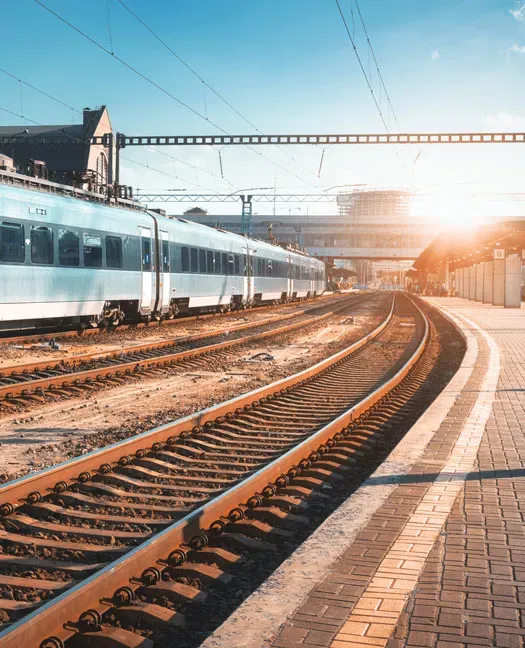
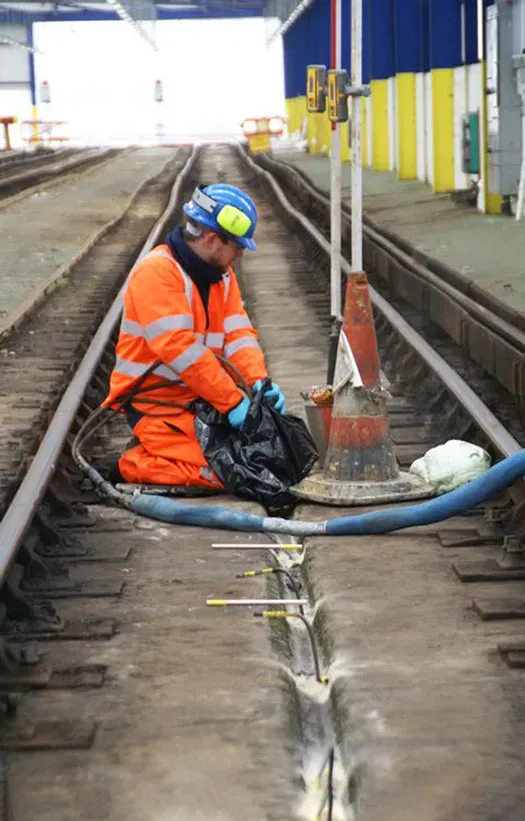